Minimalmengenschmierung MMS
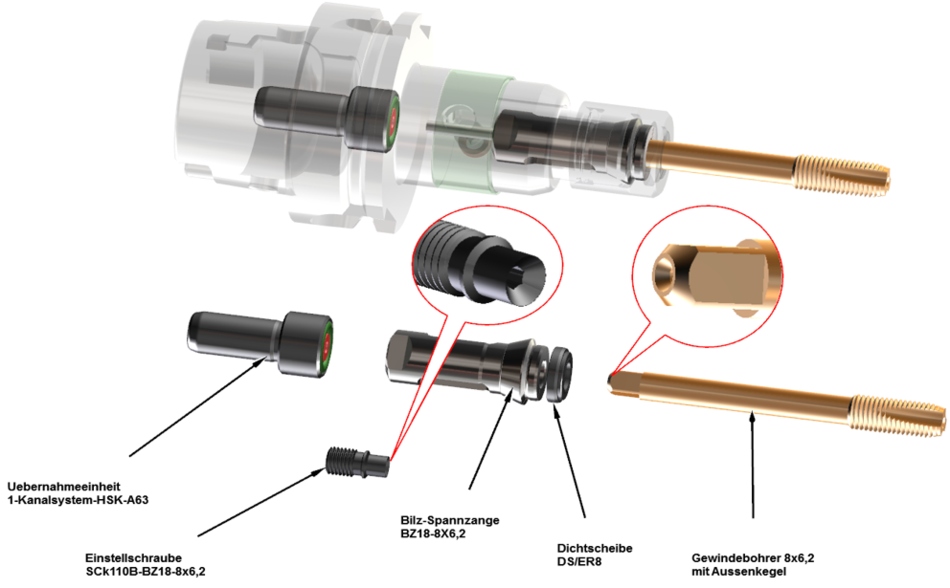
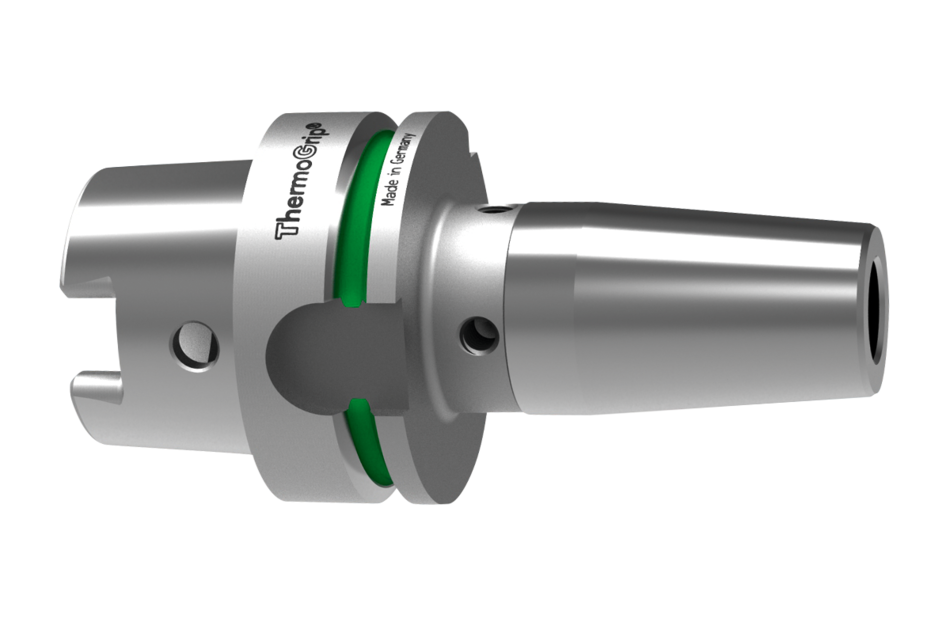
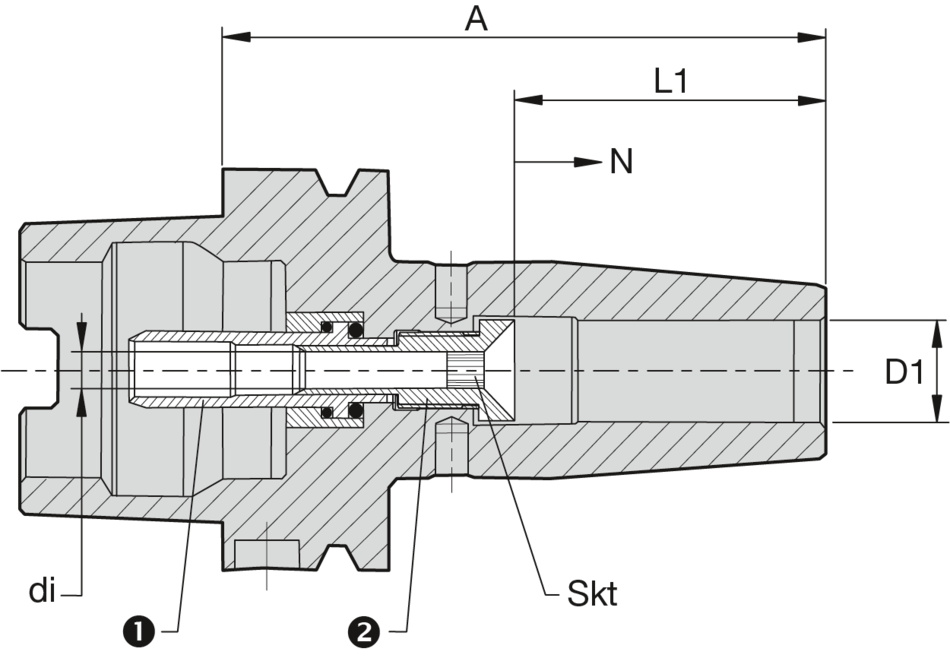
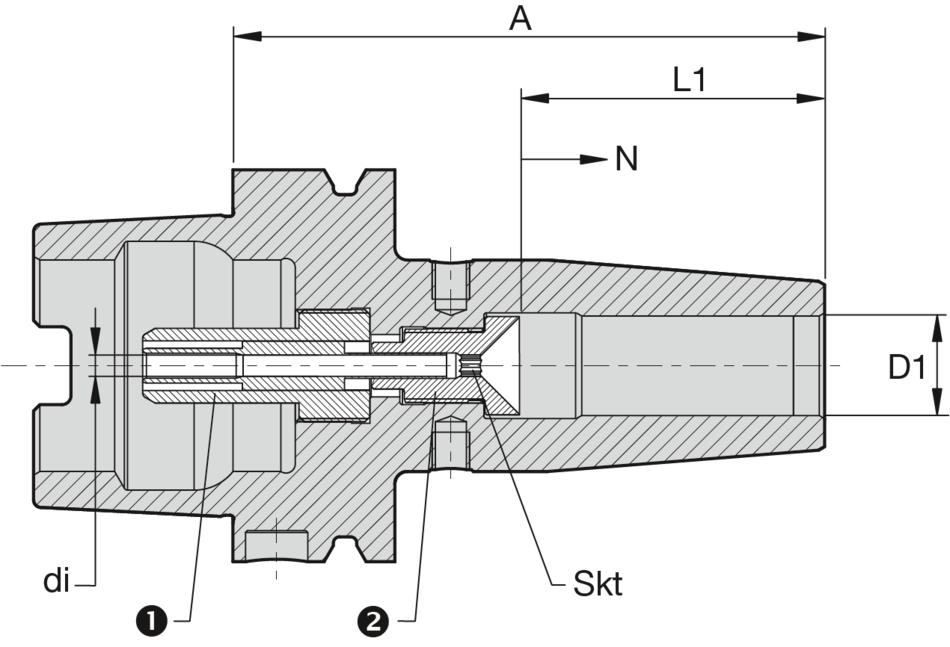
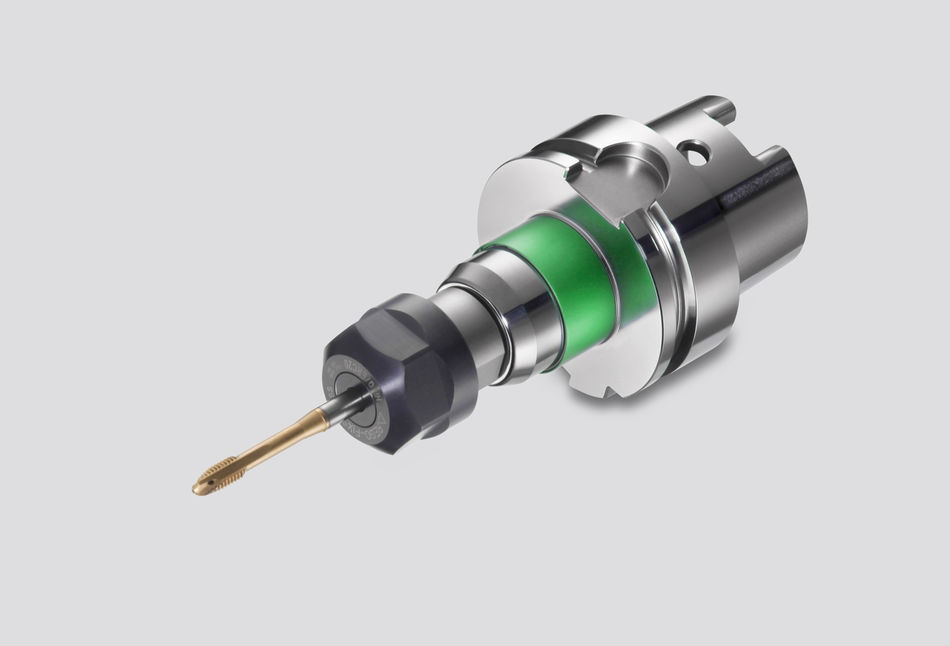
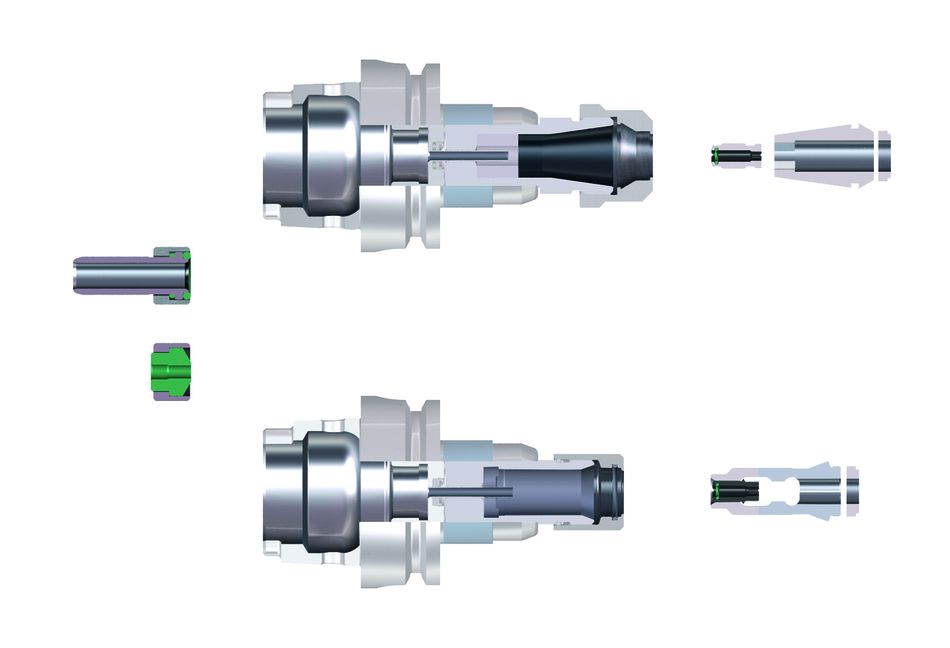
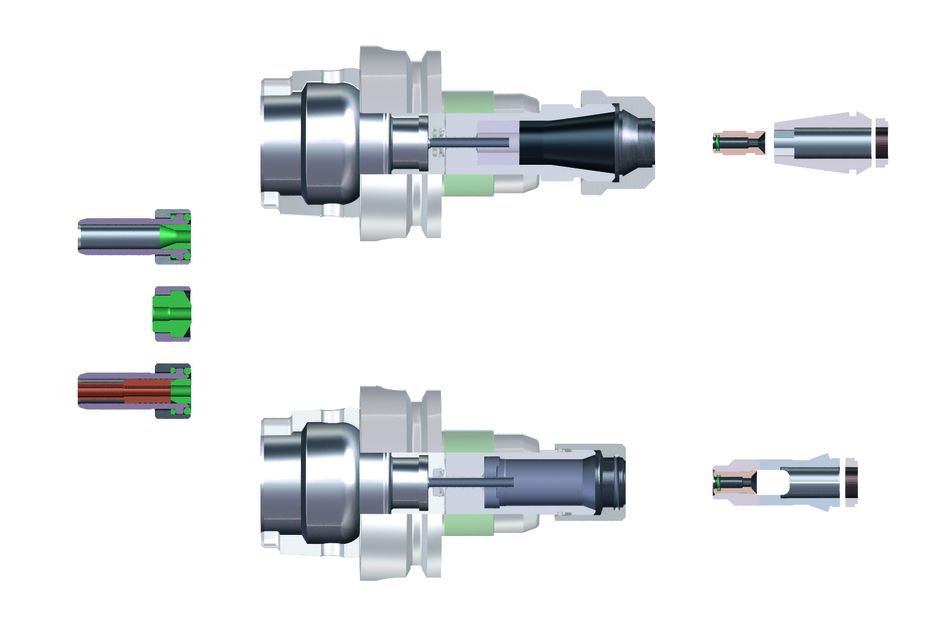
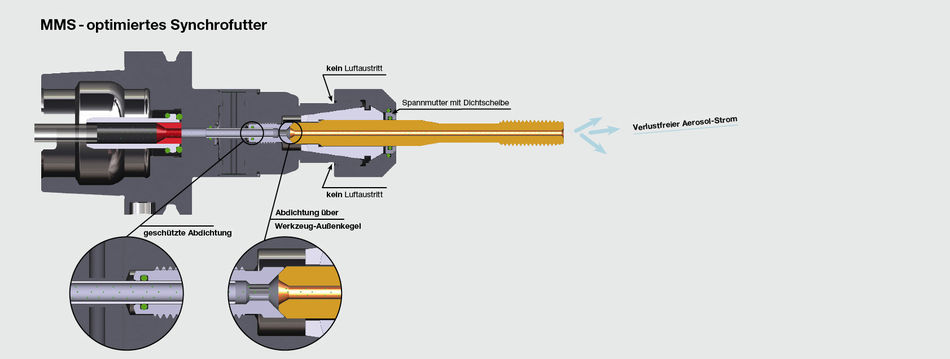
MMS - die neue Leistungsklasse MMS-fähiger Spannmittel
Schmierstoff von der ersten Sekunde an - verlustfrei!
MMS und Spannmittel
Wegen der sehr geringen Schmierstoffmenge ist es bei Minimalmengenschmierung von entscheidender Bedeutung, den Schmierstoff zielgenau und bedarfsgerecht dosiert an der Zerspanstelle aufzubringen. Hierbei spielt das MMS-fähige Spannmittel als Teil des MMS-Auftragsystems eine entscheidende Rolle.
Zukunftssichere Technologie durch Erwerb der HORKOS-Lizenz
MMS zeichnet sich gegenüber der konventionellen Nassbearbeitung durch eine enorme Verbrauchsreduzierung der eingesetzten Schmierstoffe aus.
Zwei grundlegende Herausforderungen stellen sich bei MMS an das Spannmittel:
a) Optimale Dichtigkeit für einen verlustfreien Aerosolstrom ohne Versackungen oder Austritt von Schmiermittel aus dem Spannfutter in Form von feinem Tröpfchennebel
b) Schmierstoff von der ersten Sekunde an für einen verzögerungsfreien Durchfluss des Aerosols ohne Druckabfall bis vor an die Werkzeugspitze
Die neue MMS - Generation von Bilz realisiert diese Anforderungen zu 100 %.
Die optimale Dichtigkeit unserer Synchrofutter ist bisher einmalig auf dem Markt und wurde im Januar 2010 zum Patent angemeldet.
Synchrofutter S3D - the next generation
Prozessoptimierung durch Innovation
Der minimale Längenausgleich auf Druck und Zug kompensiert kleinste Lageabweichungen bei Synchronisationsfehlern der Maschine. Der Flankendruck und dadurch auch der Verschleiß an den Gewindeflanken wird so erheblich verringert - für deutlich höhere Standzeiten, bessere Gewindequalität und verschleißfreies Arbeiten.
Kombi-Lösung MMS, IK und Trockenbearbeitung - ein Futter genügt
Kühl- und schmiermittelzufuhrunabhängig eignet sich das S3D generell für:
• MMS-1-Kanal/MMS-2-Kanal (optional)
• IK bis 50 Bar Kühlmitteldruck
• Trockenbearbeitung
• Maschinen mit manuellem oder automatischem Werkzeugwechsel
Kombi-Lösung beidseitige Längennachstellung - praktisch ein Handgriff
Die Längennachstellung kann flexibel sowohl von Werkzeug- als auch von Maschinenseite her erfolgen – ein Eingriff statt zeitintensives Nachkorrigieren.
Kompakte Konstruktion - noch mehr Sicherheit
Bis zu 100% verbesserte Standzeiten durch konstant hochwertiges Schneidverhalten bei langer Lebensdauer und einfachster Montage:
• Leerlaufdrehzahlen bis 15.000 min-1
• kompakte Konstruktion
• formstabile verschleißfreie Elastomer-Teile
• minimaler Längenausgleich (Druck/Zug +/- 0,15 mm)
Weiterdenken! Die zukunftssichere Minimalmengenschmierung mit BILZ
Das Verfahren der Minimalmengenschmierung (MMS) wird immer wichtiger. Als zuverlässiger Partner seiner Kunden sichert sich BILZ schon heute den Zugang zu den Technologien von morgen und hat die Lizenz zur Verbindung im Futter von HORKUS aus Japan erworben. Warum gerade diese Maschinen-/Werkzeugschnittstelle von zentraler Bedeutung ist, erklären wir im folgenden Artikel. ….Mehr/Weiter
Weiterdenken! Die zukunftssichere Minimalmengenschmierung mit BILZ
Das Verfahren der Minimalmengenschmierung (MMS) hat in den letzten Jahren bei der spanenden Bearbeitung an großer Bedeutung gewonnen. Die MMS bezeichnet dabei grund-sätzlich das Schmieren von Zerspanungsprozessen mit geringen Mengen Schmiermittel. Die Vorteile in der Bearbeitung liegen klar auf der Hand:
-Verlustfreier Aerosolstrom bis vor an die Werkzeugspitze
-Verzögerungsfreier Durchfluss des Aerosol ohne Druckabfall
-Flexible Systeme für Gewindeschneidsysteme und Schrumpfaufnahmen
-Zukunftssichere Technologie durch Erwerb der HORKUS-Lizenz
Bei der MMS kommt ein Luft-/Ölgemisch zum Einsatz, welches durch optimale Schmierung die Entstehung von Reibungswärme verhindert. Die restliche Wärme wird über das Werkzeug und den Span abgeführt. Historisch gesehen löste bei der Kühlung der Bearbeitungsstelle die Zufuhr von Kühlschmiermittel (KS) von außen über die Maschine durch das Futter die Zufuhr von KS von außen ab. Die Innere Kühlmittelzufuhr (IK) war geboren und bestand im Wesentlichen aus Wasser mit einem geringen Anteil Schmierstoff, durchgeleitet mit einem Druck von 50 bis 80 bar. Allerdings zeigten die Erfahrungen von Großserienproduzenten, dass die IK einen Anteil von bis zu 15 Prozent an den Fertigungs-kosten ausmachte. Daraus entstand die Idee der MMS, denn der „normale“ Verbrauch von teilweise mehreren Hundert Litern Wassern pro Stunde war ökologisch und ökonomisch nicht zukunftsfähig. Der Schmierstoff wurde nun nur noch in geringem Umfang zugeführt und man ließ das Wasser einfach weg. Statt des Kühlschmiermittels nimmt man z.B. nur noch den Schmierstoff Öl, welcher fein zerstäubt als Nebel (Aerosol) bei einem Druck von 6 bis 10 bar zugeführt wird. Heutige MMS-Systeme haben einen Verbrauch von kleiner 100 Millilitern pro Stunde, manche sogar weniger als 10 ml.
BILZ bietet 1- und 2-Kanal-Systeme
Die Technologie der MMS wird in zwei Systeme unterteilt, BILZ bietet beide Systeme für Synchroaufnahmen und Schrumpfaufnahmen: Es gibt die äußere MMS-Zuführung, bei der dem Werkzeug bzw. der Wirkstelle die Minimalmenge durch eine im Bearbeitungsraum der Maschine installierte Düse zugeführt wird. Und die innere MMS-Zuführung, wobei diese hier durch die Arbeitsspindel, die Werkzeugaufnahme und das Werkzeug direkt bis in die Schneide erfolgt. Das ermöglicht eine optimale Benetzung an der Eingriffsstelle. Innerhalb der MMS-Systeme wird wiederum in 1-Kanal- (Vormischung des Aerosols außerhalb der Spindel) und 2-Kanal- (Vormischung direkt in der Spindel) Verfahren unterteilt. Heutzutage hat die 1-Kanal-Technologie deutlich die Nase vorn. Das Aerosol wird so fein zerstäubt, dass es sich praktisch nicht mehr entmischt. Damit sind auch längere Zuleitungen und auch „Ecken“ kein Problem mehr, von der Ansprechzeit des unter Druck stehenden Aerosols, der einfachen Handhabung und den damit verbundenen geringeren Kosten ganz zu schweigen.
Positive Effekte auf Wirtschaftlichkeit, Umweltfreundlichkeit und Arbeitsschutz
Die MMS kann aber noch viel mehr und schlägt auch finanziell stark positiv zu Buche: Sämtliche Ver- und Entsorgungstechnik für den Kühlschmierstoff entfällt, die Standzeiten sind optimiert und die Prozessdauer sinkt um bis zu 30%. Zudem muss das KS nicht mehr geprüft und gepflegt werden und das Reinigen der Werkstücke wird reduziert. Und ökologisch macht das auch Sinn: Es fallen keine umweltschädlichen Altemulsionen an und Unfälle durch auslaufende KS sind auch nicht mehr möglich. Zudem hat die MMS auch ein großes Plus für den Arbeitsschutz, denn ein trockenes Maschinenumfeld erhöht die Arbeitssicherheit und durch KS verursachte Erkrankungen z.B. der Atemwege gehören auch der Vergangenheit an. Gibt es also nur Vorteile? Keineswegs, denn die täglichen Herausforderungen sind komplex. Der Wegfall von Wasser bedeutet in letzter Konsequenz, dass die Bearbeitungsstelle nicht mehr gekühlt wird, die Späne werden nicht mehr durch das KS „weggeschwemmt“, sondern bleiben in der Maschine oder am Werkstück bzw. Werkzeug kleben und auch die Zufuhr von Aerosol durch Maschine, Futter und Werkzeug ist nicht einfach.
Die MMS als zukunftssichere Technologie von BILZ
Was ist also zu tun und was bedeutet dies für einen führenden Futter-Hersteller wie BILZ? Ganz einfach ausgedrückt: Die Anpassung aller Komponenten an die MMS-Bearbeitung, und zwar von allen Beteiligten:
-Hinsichtlich der Maschinen wird eine neue Technik bei der Abfuhr der Späne und bei der Zufuhr des Aerosols benötigt.
-Die Schnittparameter der Bearbeitungsprogramme müssen so konfiguriert sein, dass keine Überhitzung auftritt.
-Bei den Werkzeugen können Änderungen der Kühlkanäle notwendig werden.
-Im Futter selbst muss für eine sichere Durchleitung des Aerosols gesorgt werden und das Aerosol selbst muss sicher durch die MMS-Geräte bereitgestellt werden.
Große und vielfältige Anforderungen, denen sich BILZ täglich stellt, um an der optimalen und vor allem zukunftssicheren Lösung für den Kunden mitzuarbeiten. Das macht es umso wichtiger, dass man mit seinem einzigartigen technologischen Baukastensystem voraus denkt und mit allen führenden MMS-System-Herstellern die notwendigen patent- und lizenzrechtlichen Vereinbarungen frühzeitig trifft, um die relevanten Systeme auch nutzen zu können. Das gilt vor allem für das zentrale Patent der MMS zur Verbindung im Futter von HORKUS aus Japan. Hier hat BILZ die Lizenz erworben, um als zuverlässiger Partner unseren Kunden stets die zukunftssicherste Technologie zu bieten.
Ansprechpartner
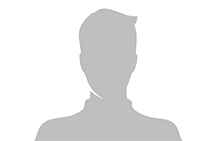